Welding automation addresses labor concerns in heavy industries
- Green Denmark in Southeast Asia
- Feb 21, 2023
- 3 min read
Contribution by Philip Toft Halskov
The growing need for skilled welders in offshore wind and shipyards in Singapore has placed a huge demand for labor in these sectors. Numerous manufacturers experience a lack of efficient, high quality welding solutions for large and complex structures.
For example, some wind projects can span two to three years, and a single project can easily require 100 full-time welders on the job as structures are increasing in both size and complexity.
Ask just about anybody involved in manufacturing about hiring, and they’ll probably all eventually say the same thing: a good welder is hard to find.
Actually, any welder is hard to find.
The years-long shortage of welders is showing no signs of easing up. According to Singapore Welding Society, the gap between jobs and the number of people needed to fill them will hit 75,000 in 2023. By 2026, the shortage is projected to grow to 150,000.
As a result, manufacturers are doubling down on their efforts to expand training options and secure partnerships with training schools. Older welders are also reaching retirement age, and the younger generation are not replacing them fast enough. In fact, the average age of a welder is 55, and fewer than 20 percent are under the age of 35.
Access to a skilled, proven welding workforce has never been more important. As the nation’s infrastructure continues to age, construction contractors will be required to rebuild structures, bridges and roadways. Skilled welders will also be an asset to the offshore wind and oil and gas industries, where they work on pipelines, wind turbines and other energy delivery sources.
For offshore wind contractors, one of the biggest challenges is finding skilled and experienced welders to complete the project on time, within budget and to the highest quality standards. If deadlines are not met, contractors will usually have to pay for liquidated damages.
Solutions to improve weld quality and productivity
Nonetheless, these challenges can be addressed if the right solutions are implemented - welding solutions that can replicate the skills of a manual welder and provide a method that has the ability to follow an approved procedure, and plan the sequence just like a welder would do, as well as producing high quality work.
To address these challenges and meet project deadlines with a shrinking pool of skilled welders, Inrotech has developed the Inrotech-Vertigo that offers several advantages to traditional gantry-based solutions; lower cost, less transport of large structures and flexibility to move to a variety of working zones. Rasmus Faudel, System & Software Manager of Inrotech explains
“we specialize in bringing the robot to the job, rather than the traditional method of bringing the job to the robot. This philosophy is the only way you can achieve automated welding on some of the very large structures we now experience in offshore and wind markets."

The Inrotech-Vertigo is a portable platform with a robot installed on double vertical axis, capable of welding vertical multi-pass welds. It is capable of reaching up to approximately 4.5 meters above ground level, and is therefore suitable for working on large structures, where manual welders normally spend hours setting up scaffolding.

Figure 1 Inrotech-Vertigo scanning the groove onsite
It features Inrotech’s unique WeldLogic Technology and runs fully automatic throughout the entire process. The robot first locates, scans and analyzes the welding groove, thereafter, plans and performs the weld without any interaction required from the operator, as the scanning procedure automatically feeds that information into the system.
During the welding process the robot automatically cuts the wire, cleans the welding torch and deslags the groove with a separate needle hammer tool to ensure a perfect weld. Additionally, the robot ensures that the temperature stays within the customer’s specifications.
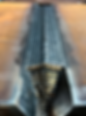
For more information, please contact Philip Toft Halskov, pth@inrotech.com